Solar cable is a special cable used to connect PV modules and inverters, which is UV resistant, corrosion resistant, abrasion resistant, etc. It can adapt to indoor and outdoor use under different environmental conditions. Here is the production process of solar cable.
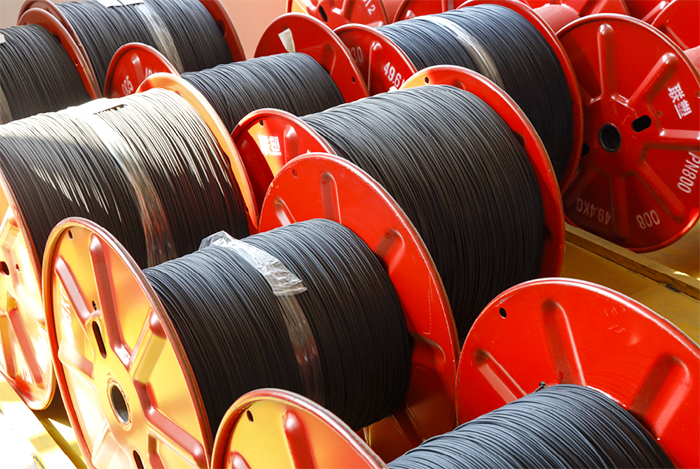
Step 1: Purchase and preparation of raw materials
The main materials of solar cable are conductor, insulation and sheath. Conductor is the current conduction part, you can choose copper or aluminium as the conductor material; insulation is used to prevent the current loss of a layer of film, usually using special polyolefin as the material, the sheath is to protect the cable from the external environment of the erosion of the commonly used materials are polyvinyl chloride (PVC) and polyethylene (PE).
Step 2: Manufacture of the conductor
The conductor is the part that carries the current and is usually made of copper or aluminium. In the manufacturing process, the raw material of copper or aluminium is melted and then extruded into cylindrical conductors of different diameters by means of special extruders.
Step 3: Manufacture of the insulating layer
Insulation is a thin film used to stop the loss of electrical current. The insulation is usually made from a special polyolefin material, which is melted and extruded into a film using extrusion technology, and then wrapped around the conductor using a special process.
Step 4: Sheath Manufacturing
The sheath protects the cable from the elements and is usually made from PVC or PE. To manufacture the sheath, the PVC or PE material is melted, then extruded into a tube by extrusion technology, and finally the tubular sheath is placed over the conductor.
Step 5: Cable Assembly
The conductor, insulation and sheath are assembled together to form the finished cable. In the assembly process, the insulation layer is put on the conductor first, and then the sheath is put outside the insulation layer.
Step 6: Testing
Test the finished cable to ensure that the conductivity, insulation and waterproof performance of the cable meet the standard requirements. Test items include conductivity test, voltage resistance test and appearance inspection.
The above is the production process of solar cables, by strictly controlling each production link, we can ensure the quality and reliability of solar cables to meet the requirements of solar power generation system.
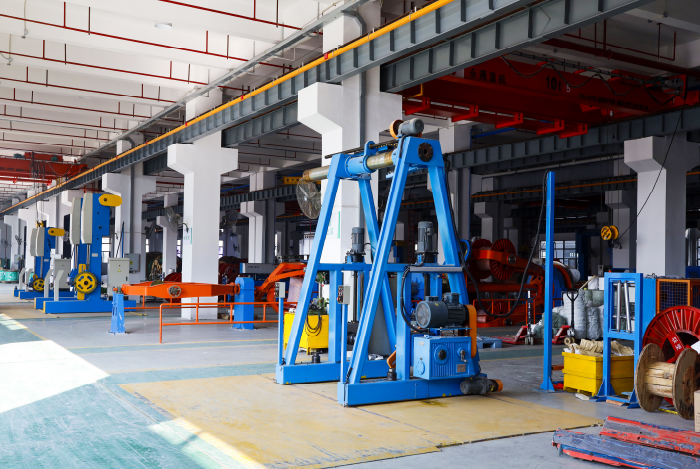
Birth of Solar Cables
The manufacturing process of solar cables involves several steps to ensure the electrical performance, durability and safety of the cables. The following are the main processes involved in the production of solar cables.
1. Preparation of raw materials: First of all, you need to prepare the raw materials required for cable manufacturing, including conductor cores, insulation materials, sheath materials and so on. Firstly, the raw materials required for cable manufacturing need to be prepared, including conductor cores, insulation materials, sheath materials, etc. The conductor cores are usually multi-stranded. The conductor core is usually multi-stranded copper or aluminium wire, the insulation material can be weather-resistant polyvinyl chloride (PVC) or polyethylene (PE) and other materials, the sheath material can be weather-resistant rubber or polyvinyl chloride (PVC) materials.
2. Conductor core preparation: The raw materials for drawing, annealing, stranding and other processes. Drawing, annealing, stranding and other processes to prepare the required conductor core. Conductor core preparation is one of the key steps in the production of solar cable, its quality and performance directly affect the electrical performance and durability of the cable.Insulation preparation: in the conductor core outside the insulation layer. Insulation layer preparation can be used extrusion, winding, impregnation and other processes to ensure the electrical performance and weather resistance of the cable. In the extrusion process, usually using high temperature, high pressure way to melt the insulating material extrusion in the conductor core, and then cooling, winding.
3. Insulation layer preparation: In the conductor core of the outside of the insulating layer. The preparation of the insulation layer can be used extrusion, winding, impregnation and other processes to ensure the electrical properties of the cable and weather resistance. In the extrusion process, usually using high temperature, high pressure way to melt the insulating material extrusion in the conductor core, and then cooling, winding.
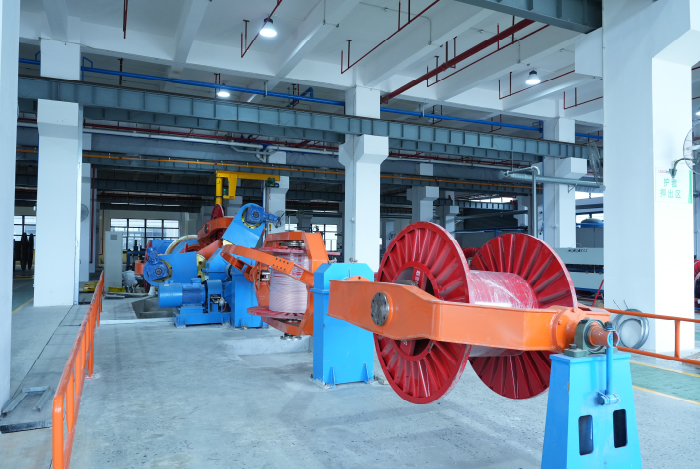
4. Sheathing layer preparation: Sheathing is wrapped around the outside of the insulating layer. Sheath layer. The preparation of the sheath layer can use extrusion, impregnation and other processes to ensure the mechanical strength of the cable, moisture, dust and other properties. In the extrusion process, usually using high temperature, high pressure way to melt the sheath material extrusion in the insulation layer, and then cooling, winding.
5. Testing and packaging: In the cable production process, a number of tests need to be carried out, including the DC resistance of the conductor core, the electrical properties of the insulation layer, the mechanical properties of the sheath layer and so on. Only the detection indexes meet the standard requirements, can be packaged. The packaging of solar cable is usually made of waterproof, moisture-proof and dust-proof materials to ensure the quality and performance of the cable during transport and use.